The future of fabrication
- Jim Mills
- 13 abr 2023
- 4 Min. de lectura
In recent years, manufacturers have had to weather a global pandemic, navigate supply chain issues, and continuously endure inflation. These manufacturers, which are the foundation of the global economy, are preparing for the future by adopting advanced digital fabrication technologies to drive efficiency, gain better insights into their operations and optimize performance.
Manufacturers are eager to identify ways to automate their capabilities as they redefine their business processes amid a digital transformation. With rapidly evolving innovations in fabrication, they can deliver exceptional products and customer experiences in increasingly shorter times. In this article, we explore the future of manufacturing and the possibilities that open up ahead for companies to modernize their operations and become more flexible.
Some of the digital fabrication practices currently in place that hold promise for the future comprise 3D printing, robotics, and Artificial Intelligence. Building Information Modeling, for its ability to model the interaction between a building’s components and optimize the design for energy efficiency, among many other benefits it brings for the AEC industry, is one important asset in this list. Let’s look in more detail at some of these trends and what they have in store for the world of fabrication.
3D printing

3D printing, also called Additive Manufacturing, has come a long way since it was first developed in the 1980s as a tool for rapid prototyping. It is a method for creating 3D solid parts from a digital document, utilizing routes that incorporate materials along a physical path. Some of its contributions are the possibility of low-volume production (which comes in handy for industries such as aerospace, where highly complex parts need to be produced in low volumes), weight reduction (useful in cutting back carbon dioxide emissions from aircraft, for example) and material efficiency—since parts are produced layer by layer, the material is mostly used only where needed, with less waste involved.
Robotics

Robotics are the technology of choice for manufacturers wanting to automate tasks such as material handling, assembly, welding, handling hazardous materials, packing and shipping. Industrial robots can complete these tasks faster, improving standardization and quality and reducing operating costs. In addition, humans can experience fatigue and lose focus, which can potentially lead to errors or even injuries. Robots are easily programmable and contrary to popular belief, they may actually create jobs in the long run: programmers, engineers, designers, operators, data analysts, robot manufacturers, systems integrators, and maintenance specialists will all be required for robots to function properly.
Artificial Intelligence
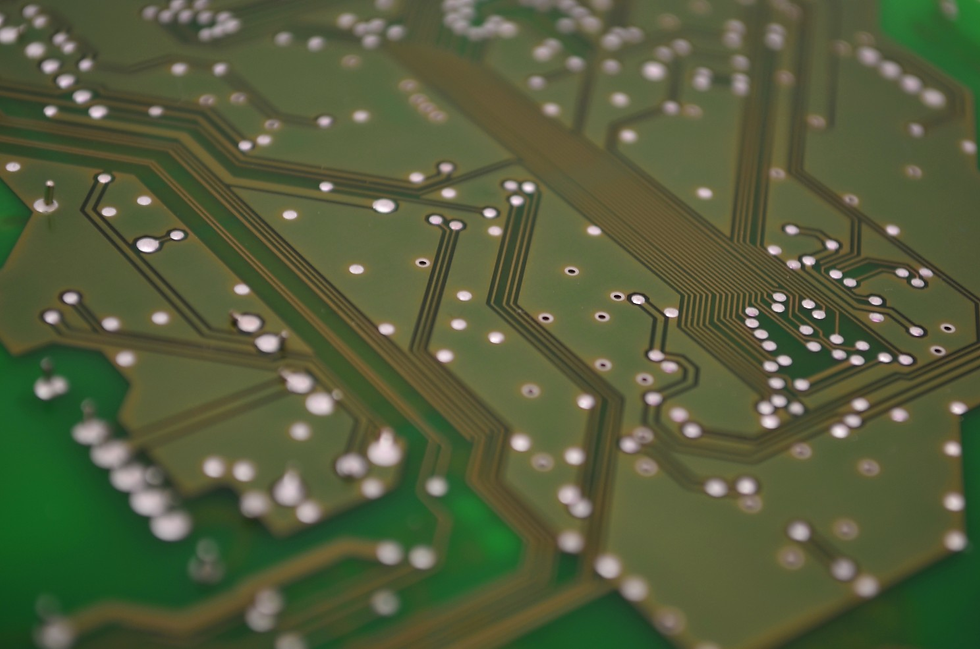
Much is being said about Artificial Intelligence, but what is its true application for the manufacturing industry? Artificial Intelligence is usually employed alongside sensors, using the data collected to predict breakdowns and prevent accidents. Through complex image processing techniques, it is also able to classify flaws across a wide range of industrial objects, thus improving defect detection and improving overall quality. AI can also guide predictive maintenance, helping production facilities in determining the likelihood of future failures in their machinery, allowing repairs to be scheduled well in advance of a breakdown. This results in less costly maintenance for production lines thanks to reduced downtime. Used in conjunction with robotics (i.e., “industrial robots”), it allows automating repetitive operations, reallocating human labor to other, more specialized activities.
BIM

As we have seen in past articles, through the notion of “digital twins”, Building Information Modeling allows for seamless collaboration between professionals working in a construction project, using a digital, three-dimensional representation of a future structure that is yet to be built. Pairing with virtual and augmented reality or integrating technologies such as drones and sensors will soon allow the methodology to grow even stronger, improving construction accuracy and precision, and harnessing the power of predictive maintenance for MEP components.
* * *
Machine Learning, IoT and the technologies surrounding sustainability are emerging trends that will most likely shape the future of fabrication. Below, you’ll find an overview of these up-and-coming developments and how they might influence the manufacturing industry in the years to come.
Machine Learning

Without explicit programming to perform a certain task, Machine Learning (a type of AI) uses data and algorithms to derive information from non-apparent patterns in a given set. This may leverage generative design, as it allows manufacturers to provide a myriad design option for a single product in considerably less time than it would take humans to produce just as many varieties. Deep Learning, as a subset of Machine Learning, analyzes moving and still images in particular, using neural networks that mimic the learning process of the human brain. This might be especially handy for performing quality inspection in industrial facilities, enabling and automating completeness and presence checks, counting, and anomaly detection, among other uses.
Internet of Things

The industrial application of IoT (Industrial Internet of Things, IIoT) implies having an interconnected system of industrial assets that uses sensors and software to collect and exchange production data. Manufacturers can control these “smart” assets to extract valuable insights from factory machines, vehicles, warehouses, facilities and inventory using a single platform. This has the potential for total automation, therefore optimizing operating efficiency and boosting productivity.
Sustainable technologies
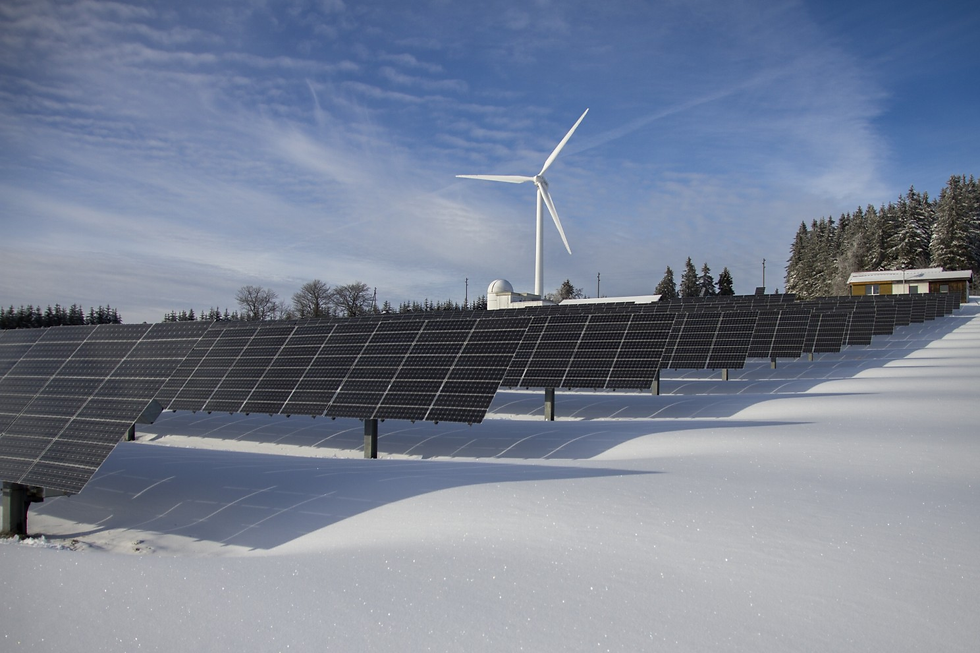
The world looks to energy efficiency, cutting back on carbon emissions and reducing waste as hope in an otherwise uncertain future. Whether mandated by governments or stemming from public demand, manufacturers will need to address these pressing issues as they struggle with a complex number of partners, distributors and suppliers within their ecosystems. Data management appears to have a major role to play, as it becomes imperative to exchange critical information with the many parties involved in all stages of production, from sourcing and fabrication, to logistics and shipping, to control any parameters that might be contributing to excess waste or emissions.
All of the technological advances we’ve seen show promise for a more streamlined industry and automated fabrication techniques that give the manufacturer full control over their production, both in terms of output as well as the implications for the entire life cycle of the product. Fortunately, the future of fabrication does not seem to be one that is solely focused on managing profit or materials, but on the responsible use of technology in order to produce the goods that humanity benefits from on a daily basis.
Comments